How a Thermocouple Functions to Measure Temperature
A thermocouple functions by leveraging the Seebeck effect, where two different metals joined together to create a voltage when subjected to varying temperatures. This generated voltage directly corresponds to the temperature difference between the heated (measuring) junction and the cooler (reference) end, allowing thermocouples to precisely measure and monitor temperatures in diverse industrial and scientific applications.
How Does a Thermocouple Work?
A thermocouple is a temperature-sensing device that operates using the Seebeck effect, a phenomenon where a voltage is generated when two dissimilar metals are joined at one end and exposed to a temperature difference. This voltage is directly proportional to the temperature difference between the hot junction and the cold junction, allowing for precise temperature measurements.
So, how does a thermocouple work in real-world applications? The generated voltage is measured and converted into a temperature reading by a thermocouple meter or an integrated control system. This simple yet effective mechanism makes industrial thermocouples an essential tool for temperature monitoring in environments ranging from cryogenic systems to high-temperature industrial furnaces.
Key Components of a Thermocouple:
- Measuring Junction (Hot Junction): The point where the two metals are joined and exposed to the target temperature.
- Reference Junction (Cold Junction): The opposite end where the metals are connected to the measuring device.
- Connecting Wires: Carry the voltage signal to the measuring instrument.
- Output Device: Converts the voltage into a readable temperature value.
Thanks to their robust construction and the variety of materials available, thermocouples can withstand extreme conditions, making them suitable for industries like aerospace, energy, and manufacturing.
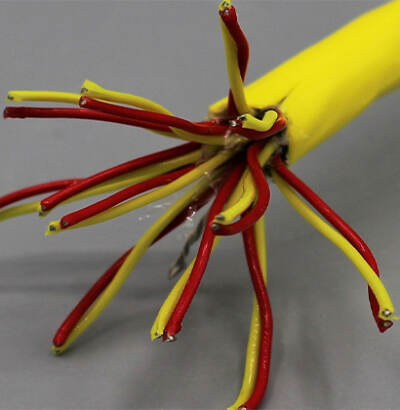
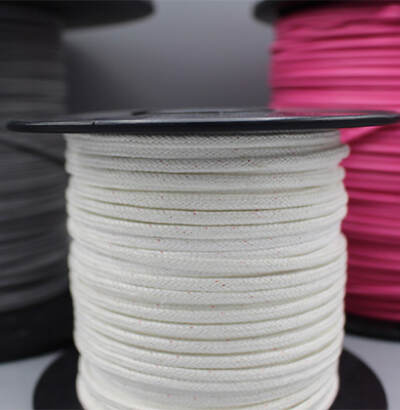
What Does a Thermocouple Do?
A thermocouple's main role is to measure temperature and provide real-time feedback for monitoring and control. Its ability to function in extreme environments makes it an essential tool for various industries.
Key Roles of a Thermocouple:
Monitoring: Consistently tracks temperature in processes like heating, cooling, and chemical reactions.
Control: Enables automated systems to adjust temperatures based on real-time feedback.
Safety: Helps prevent overheating or system failures by triggering alarms or shutdowns in critical situations.
Where Are Thermocouples Used?
Thermocouples are versatile tools with applications across various industries. Their ability to measure a wide range of temperatures, even in extreme conditions, makes them invaluable in processes that require precision and reliability. The table below highlights key industries and their uses for thermocouples:
Industry | Application | Example of Use |
---|---|---|
Aerospace | Engine and turbine monitoring | Measuring exhaust gas temperature in jet engines |
Manufacturing | Process control | Monitoring heat during metal forging or welding |
Energy | Power plant operation | Monitoring boiler and steam turbine temperatures /td> |
Food & Beverage | Quality control | Ensuring proper cooking and pasteurization temps |
Research & Development | Experimental setups | Measuring reaction temperatures in lab settings |
Why Calibrating Thermocouples Matters
Regular calibration of thermocouples is essential to maintain their accuracy and reliability. Over time, factors such as material degradation, environmental exposure, and frequent use can lead to deviations in their performance. Without calibration, these deviations may result in incorrect temperature readings, potentially causing safety risks, product defects, or inefficiencies in industrial processes.
Key Reasons to Calibrate Thermocouples:
- Accuracy: Ensures temperature readings remain precise, even after extended use.
- Consistency: Provides reliable data for maintaining consistent process control.
- Safety: Minimizes the risk of equipment failure or hazardous conditions caused by incorrect temperature measurements.
- Regulatory Compliance: Meets industry standards for quality control and safety.
Calibration is typically done using a reference device with known accuracy to compare and adjust the thermocouple's readings. This process helps maintain optimal performance and extends the lifespan of the sensor.
Inspecting Your Thermocouple for Issues
Regular inspections help you catch potential problems with your thermocouple early, saving time and avoiding costly system failures. Issues like wear from high temperatures or physical damage can often go unnoticed without a thorough check.
How to Inspect a Thermocouple:
- Physical Damage: Look for cracks, bends, or breaks in the sensor or wires.
- Corrosion: Check for oxidation or discoloration on the metal surfaces, which can affect accuracy.
- Connections: Ensure all connections are tight, clean, and free of debris.
- Wire Insulation: Inspect the insulation for signs of wear or damage that could cause electrical interference.
How to Test a Thermocouple's Accuracy
Testing your thermocouple ensures it provides accurate temperature readings. Here's a quick guide:
Steps to Test a Thermocouple:
- Prepare Your Tools: Use a multimeter or thermocouple tester.
- Disconnect Safely: Detach the thermocouple from your system.
- Apply Heat: Expose the sensor to a known heat source, like boiling water or a calibrator.
- Compare Readings: Check the voltage against the expected output using a reference chart for your thermocouple type.
If readings are off, consider recalibrating or replacing the thermocouple to maintain accuracy and reliability.
Maintaining Thermocouples for Precision
Thermocouples are indispensable tools for precise temperature measurement in a wide range of applications. Regular maintenance, including cleaning, inspection, calibration, and testing, ensures they perform reliably over time. By taking these simple steps, you can maximize the accuracy and longevity of your thermocouples, keeping your systems efficient and safe.