Industrial Heating: How Long Does a Thermocouple Last?
William Nash and Eric Yeager – Cleveland Electric Labs; Twinsburg, Ohio
As a designer and manufacturer of thermocouples, the most commonly asked question we receive is: How long should my thermocouple last?
Unfortunately, the answer to this question is quite complex and is dependent on a host of variables, not all of which may be obvious. At the root of the complexity are often unseen or unanticipated factors that may have a major effect on the sensor's usable lifespan.
Essentially, every application has its own intricacies, and their impact on operational and environmental factors are not always considered or understood to specify a proper thermocouple design. To underscore the impact of often unseen or unknown factors, the following are a few application scenarios of which we have collaborated with our customers.
Application Example 1
Our first example is from an emergency call we received from a large company with multiple locations. They were suddenly seeing massive product deviations from their box-anneal operation. Their downstream product users were reporting their materials to be overheating by more than 100°F. The financial loss was substantial and growing by the day.
Responding immediately, we spent two days inspecting rows of furnaces, sensors and operational details. One of the questions asked of different operators was: "How often do you change out your Inconel protection tubes?" The operators' repeated response was: "Our preventive-maintenance schedule calls for change-out once every 12 months."
The tubes appeared to be in good condition, but upon closer examination they exhibited signs of unusual age. One of the metal protection tubes was removed from service and was cut off about 3 inches from the hot end. Looking into the cut piece, the tube appeared as a clogged artery lined with plaque. There was a very thick lining of inky-black carbon. This indicated that the tube had not been replaced in several years.
Upon reviewing the maintenance logs, it was discovered that there was a lapse in tube replacement going back over three years. In effect, new thermocouples were installed into contaminated tubes, causing the degradation of the sensors and generating greater than a 100°F shift in accuracy. In this scenario, thermocouple life, which should have been close to one year, was shortened to within a week.
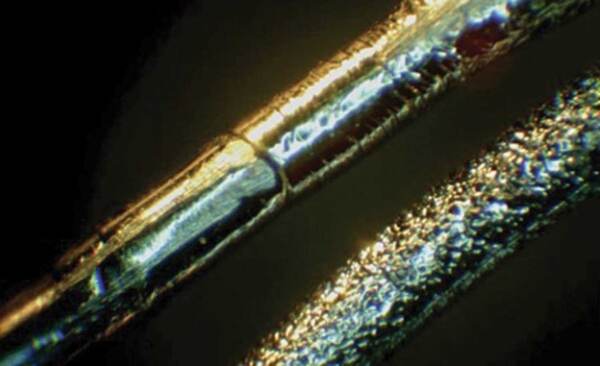
Fig. 1. Silica contamination and grain boundary slippage
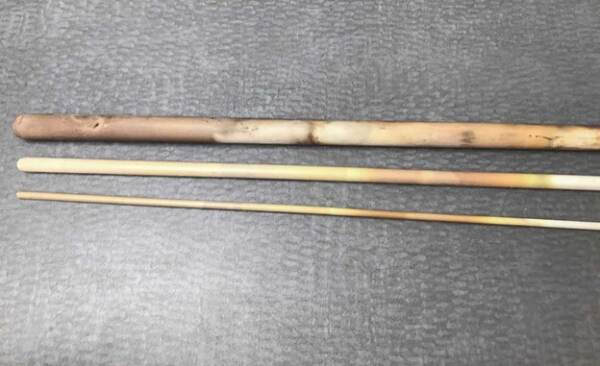
Fig. 2 Used Protection Tubes and Insulators
Application Example 2
Another example of unseen forces impacting the accuracy and life of a thermocouple occurred in a large steel operation. Out of the blue (or so it seemed), our customer was experiencing rapid failures of their high-value, Type-R platinum thermocouples. The situation was promptly investigated, and it was found that the internal conductor wires were melting near the junction. This is an unmistakable sign of silica contamination causing eutectic formation, which allows platinum to melt at very low temperatures (Fig. 1).
Upon inspection, we found zero evidence of silica (SiO2) in the furnaces, and our customer believed they had made "no changes" in their operation in over a decade. Through a collaborative, open dialogue, we identified they were in fact now treating a product containing silica. As it turned out, the steel composition had seen a major change, which included a significant silicon content. Based on that revelation, a thermocouple was designed that was better suited to resist the infiltration of the silica, thereby protecting and extending the life of the assembly.
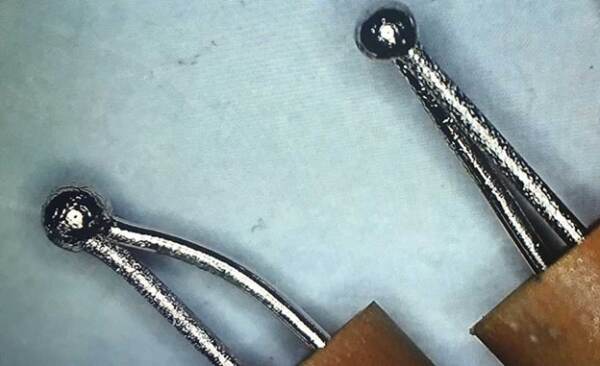
Fig. 3. Used protection-tube contamination on new elements
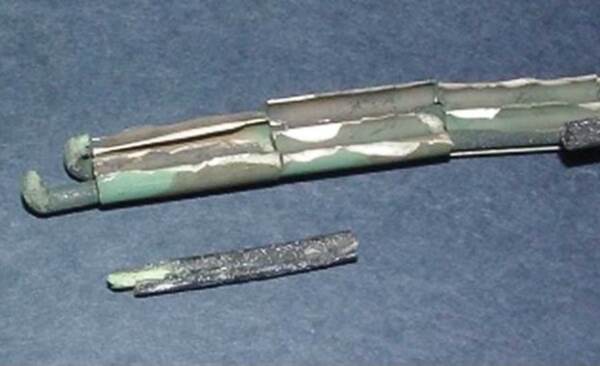
Fig. 4. Green rot on Type-K elements
Application Example 3
A final example for consideration was at an established steel-forging operation whose maintenance routine was to replace their Type-S elements every six months of operation. The customer was not getting their expected six-month life out of their Type-S elements and would see up to an 80°F drop in thermocouple output, which caused their furnace to go into an over-temperature condition.
Through a mutual investigation, we focused on the replacement frequency of the protection-tube assembly, which contained both a primary and secondary alumina protection tube. The maintenance protocol established by the customer was replacement "only when they crack or break."
In this scenario, placing the brand-new element in the used protection-tube assembly (Fig. 2) immediately started the contamination process once the heat was applied. Depending on how contaminated the used assembly was, the accuracy and longevity of the new element was negatively affected at an accelerated rate. The infrequency of replacement resulted in immediate contamination of the new thermocouple element (Fig. 3). In this scenario, the perceived savings of the protection-tube replacement protocol resulted in significant loss due to reduced thermocouple life, accuracy and product quality.
What we Learned
The common denominator in each of these scenarios is that small, seemingly insignificant and/or innocuous changes were having a major effect on thermocouple performance. There are a host of parameters that end users need to know up-front when considering expected thermocouple life. These include:
- What is the probe diameter?
- What thermocouple type is going to be used (K, N, S, B, etc.)?
- What is the operating temperature?
- Does the furnace run at a constant temperature?
- Does the furnace see frequent heating and cooling cycles?
Smaller-diameter sensors react more quickly but are also consumed at a faster rate. A steady temperature will enjoy longer life, a cycling thermocouple will see shorter life and higher temperatures degrade a thermocouple more quickly. These are just a few of the operational factors that must be considered.
Operational/Environmental Considerations
Additionally, environmental conditions also impact thermocouple selection. Platinum-based (also known as noble-metal) sensors such as Type R, S or B can be very accurate over an extended period if properly protected. Noble-metal thermocouples inherently have a very low EMF (electromotive force) output, however. Even the slightest contaminant may influence the microvolt output of the sensor, thereby altering the readings. To ensure longevity and continued accuracy, protection from elements – platinum poisons such as carbon or silica – may require specialized protection tubes, sealants and/or coatings to guarantee those elements do not migrate through and contaminate the measuring wires. Even the geographic furnace location (in terms of elevation above sea level) has a minute but measurable effect on thermocouple output.
Base-metal elements such as Type J or K have their own special operational/environmental requirements as well. For example, a Type-J thermocouple element contains an iron leg that may become oxidized at higher temperatures. Type K elements, when installed inside undersized protection tubes in temperatures in excess of 1400°F and a low concentration of oxygen, may experience a condition known as "green rot," where the conductors will turn green and become embrittled (Fig. 4). A typical solution to green rot is simply selecting a protection tube with a larger inside diameter, which allows the Type-K element to "breathe." Use of base-metal elements insulated in MgO (i.e., MIMS – mineral-insulated metal-sheath) can virtually eliminate those effects due to the encapsulated, hermetically sealed configuration of the thermocouple wires internal to the metal sheath.
We all want to know how long our thermocouples should last, but the attention to detail is critical. As a designer and manufacturer of the thermocouple, this means we need a very careful and thorough review of all the operating parameters, even the host of tiny details that may seem innocuous or insignificant.
Customers are demanding improved accuracy, longer life, stringent quality and strict adherence to specifications. The only way to stay ahead of this industry-wide consistent pursuit is to collectively and thoroughly understand the operating parameters.
All things considered, the question remains, "How long should my thermocouple last?" The answer to that question is that it depends on the application. In an ideal environment, that length of time can be indefinite. But as reality dictates, particularly in thermal processing, that is not necessarily the case. So, there are questions we need to ask ourselves when choosing a thermocouple assembly. Those questions include, but are not limited to:
- Where is the thermocouple going to be used?
- What type of furnace?
- What is the atmosphere in the furnace? Gas-fired? Hydrogen?
- What is the thermal cycle of the process?
- Is the temperature constant, or are there ramps, dwells and quench?
- What material(s) is/are being processed?
- What type of heating elements?
- What is the expected thermal profile?
- What is the temperature accuracy/furnace class?
- What is the required life expectancy, and is that life realistic for the application?
- Will the probe move, or will it be stationary?
- Is there a power line anywhere near the thermocouple leads?
- How far away is the controller or PC that receives the input?
We know the questions to ask and variables to be studied are considerable, but they are relevant factors that need to be considered when determining the best thermocouple assembly for the application. We are all facing increasing pressure and expectations to maximize the efficiencies of processes, and we need to consider those factors when selecting thermocouples.
Best practices and longevity are determined by the aforementioned conditions, but ultimately how long a thermocouple will last is best determined by historic use within the organization. Additionally, the longevity should be reconsidered each time a change is made in a process no matter how minor that change may be.
Conclusion
The best guidance is to utilize the experience and knowledge of your thermocouple supplier to guide you through the selection process. Secondarily, utilize the excellent reference source of thermocouple applications in the ASTM (American Society for Testing and Materials) Manual on The Use of Thermocouples in Temperature Measurement, MNL 12.