What Are Different Types of Thermocouples?
Thermocouple History
Thermocouples function based on the fundamental principle known as the Seebeck effect, discovered by Thomas Johann Seebeck in 1821. This effect elucidates the generation of an electromotive force (EMF) or voltage when two dissimilar metals are connected at two junctions, and there exists a temperature gradient between them. In the context of thermocouples, one of these junctions is designated as the measurement junction or hot junction, where the temperature is being assessed, while the other serves as the reference junction or cold junction. The temperature difference between these junctions leads to the creation of a voltage across the thermocouple wires. This voltage, typically in the millivolt range, is proportionate to the temperature disparity and forms part of a thermoelectric circuit. The output voltage is measured using instruments like a voltmeter, and its conversion to temperature is achieved through standard reference tables or mathematical equations specific to the thermocouple type. Renowned for their simplicity and reliability, thermocouples find extensive use across diverse industries for temperature measurement and control applications.
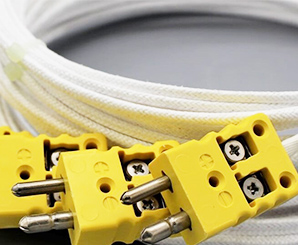
Different Types of Thermocouples:
Thermocouples come in various types, each designed for specific temperature ranges and applications. Here are some common types of thermocouples, identified by letter codes:
1. Type K (Chromel/Alumel):
This is one of the most widely used thermocouples. It consists of a positive leg made of chromel (alloy of nickel and chromium) and a negative leg made of alumel (alloy of nickel, aluminum, and silicon). K type thermocouples covers a broad temperature range and is known for its reliability and versatility.
2. Type J (Iron/Constantan):
Type J thermocouples have a positive leg made of iron and a negative leg made of constantan (copper-nickel alloy). They are suitable for a moderate temperature range and are commonly used in industrial applications.
3. Type T (Copper/Constantan):
T type thermocouples have a positive leg made of copper and a negative leg made of constantan. It is well-suited for low-temperature applications and offers good accuracy.
4. Type E (Chromel/Constantan):
Type E thermocouples consist of a positive leg made of chromel and a negative leg made of constantan. They are known for their high sensitivity at low temperatures and are often used in cryogenic applications.
5. Type N (Nicrosil/Nisil):
N type thermocouples utilize nicrosil (nickel-chromium-silicon) for the positive leg and nisil (nickel-silicon) for the negative leg. They offer high stability and accuracy across a wide temperature range.
6. Type S (Platinum/Rhodium):
Type S thermocouples feature a positive leg made of pure platinum and a negative leg made of platinum alloyed with 10% rhodium. These thermocouples are commonly used for high-temperature applications, such as in the range of 0 to 1600°C.
7. Type R (Platinum/Rhodium):
Similar to Type S, R type thermocouples use platinum for both legs, with a platinum alloy containing 13% rhodium. They are also suitable for high-temperature measurements.
8. Type B (Platinum/Rhodium):
B type thermocouples use platinum for both legs, with one leg alloyed with 30% rhodium and the other with 6% rhodium. They are designed for extremely high-temperature applications, often exceeding 1700°C.
9. Type G (Nickel/Copper/Aluminum):
G type thermocouples consist of a combination of two different alloys: one containing 94% nickel and 6% copper (Ni-Cu) and the other containing 97% copper and 3% aluminum (Cu-Al).
10. Type M (Nickel/Nickel-Copper):
Type M thermocouples are frequently utilized in vacuum and reducing atmospheres, and they are also appropriate for oxidizing environments. Their operational temperature spans from about -200°C to 1,400°C (-328°F to 2,552°F).
Thermocouple Type Choice
The choice of thermocouple type depends on factors such as the temperature range of the application, environmental conditions, and required accuracy. Each type has its advantages and limitations, making it essential to select the appropriate thermocouple for specific use cases.
One of the key advantages of thermocouples is their broad temperature range. With varieties tailored for specific temperature ranges, these sensors can operate from extremely low temperatures in cryogenic applications to high temperatures encountered in industrial processes. The versatility of thermocouples makes them indispensable in sectors such as manufacturing, aerospace, healthcare, and energy.
Moreover, thermocouples are renowned for their durability and ruggedness, making them well-suited for harsh environments. Their simple construction, devoid of fragile components, contributes to their resilience against mechanical stress, vibrations, and corrosion. This robustness ensures the reliability of temperature readings in demanding settings, enhancing the overall efficiency and safety of industrial processes.
Thermocouples find extensive use in temperature monitoring and control systems. Industries such as metallurgy, petrochemicals, and food processing rely on thermocouples to ensure optimal operating conditions and product quality. In scientific research, these sensors are invaluable for experiments requiring precise temperature control.
Recent advancements in materials and manufacturing techniques have led to the development of innovative thermocouple designs, enhancing their accuracy and response times. Additionally, digital thermocouples equipped with advanced signal processing capabilities contribute to more efficient data acquisition and analysis.
The ubiquity of thermocouples stems from their simplicity, durability, and wide applicability across diverse temperature ranges. Whether in industrial processes, scientific research, or everyday applications, thermocouples continue to be indispensable tools for accurate and reliable temperature measurement.